- By
- Posted Monday, January 20, 2020 - 09:15
Aircraft flight test has traditionally been expensive and time consuming to accomplish, requiring complex hardware design and integration and extensive operational test teams to address aircraft downtime for instrumentation maintenance and calibration,
Dan O’Neil, LORD MicroStrain®
Steve Low, Boeing Military Aircraft
Background
Aircraft flight test has traditionally been expensive and time consuming to accomplish, requiring
complex hardware design and integration and extensive operational test teams to address aircraft
downtime for instrumentation maintenance and calibration, flight operations, and post-flight data
handling and evaluation.
Recently, elements of Boeing Military Aircraft flight test and LORD MicroStrain worked jointly
to conduct a flight load, vibration, and thermal survey of a Boeing S-100 autonomous rotorcraft
using a suite of MicroStrain wireless sensors and inertial devices. This program
represents a technology breakthrough wherein an autonomous rotorcraft flight test program
utilized only wireless sensors within synchronized networks to collect flight data of interest.
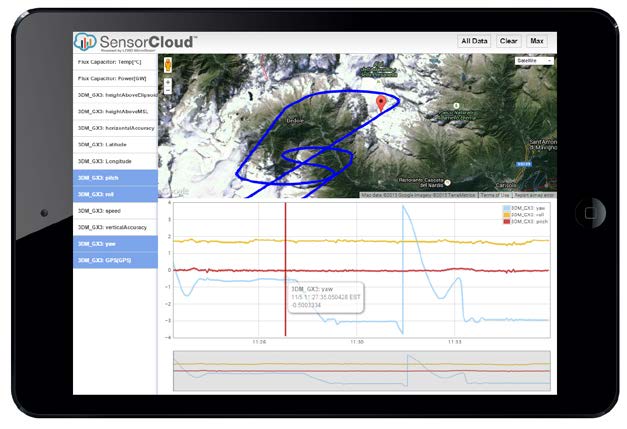
In addition to the successful collection of high quality data, the Boeing team was able to
accelerate the flight test program with significantly reduced expense by leveraging off-the-shelf
wireless technology. The wireless nature of the comparatively affordable technology allowed a
minimally-invasive integration onto the flight vehicle, and MicroStrain SensorCloud™ analytics
enabled a single team of limited personnel to make go/no-go decisions based on nearly real-time
data evaluation. This approach provided augmented decision efficiency, which accelerated flight
test execution by allowing multiple daily sorties and concurrent data analysis.
The Aircraft
The S-100 Camcopter platform is an unmanned Vertical Takeoff and Landing (VTOL) aircraft
produced by Schiebel of Austria (Figure 1). This autonomous rotorcraft is capable of flying with
a 50 kg payload for up to a six-hour loiter time with a service ceiling of 5400m. Operators can
control the aircraft in real-time via a ground-located control station, or the aircraft can fly a
preprogrammed mission completely independent of operator intervention. Boeing Mesa is the
current US-based distributor, and it conducted a flight test program for the S-100 to better
understand and characterize effects on flight critical dynamic and structural sub-systems.